The first time I sailed was in the summer of 1961 when I was 12 years old. It was on Barton Broad in Norfolk and I was at my Grammar School's annual sailing camp, courtesy of my parents who'd stumped up the £10 fee for the week. (My Dad was earning about £20 a week as a draughtsman - probably above the national average at that time, so £10 wasn't a small amount.) The site of the School camp is still there - it's now called the Hertfordshire County Council Sailing Base, Barton Turf.
I'd read all the Arthur Ransome books by the time I was 11; I even tried to write my own version of them for the Class 4a Wall Magazine at Roebuck Junior School in Stevenage. But my experience in boats until that time had been limited to rowing on Abraham's Bosom Boating Lake at Wells-Next-The-Sea while on family holidays there (it's now a caravan site). I'd taught myself to get around under oars fairly effectively if not too elegantly. But going to Grammer School in 1960 opened a number of doors, not the least of which was the chance to learn to sail just like John, Susan, Titty and Roger. And Nancy and Peggy. And Dick and Dorothea. But mostly like the Death and Glories.
The Sailing Camp had a good number of dinghies - among them two Norfolks, two Kestrels, a Bosun, four Coypus (a local class looking like a bathtub and built from GRP), one Wayfarer, and two beautiful half deckers - Atalanta, a White Boat (a Yare and Bure One Design) and Amaryllis, equal in size and performance, but not of a class as I remember. These last two were borrowed for the week of the sailing camp from generous friends of the school, as was the Wayfarer, from a Mr Armitage, I remember.
There were also two Kayaks and a rescue boat - a twelve foot wooden clinker dinghy powered by a one and a half horsepower British Seagull outboard engine.
That first week I learned to sail, capsized a Kestel, crewed the Bosun when it capsized, and capsized and sank a Norfolk. I learned to paddle a Kayak and not to attempt to get into it by crawling along the foredeck. I also learned to run the rescue boat, and to start the Seagull - a very valuable lesson later in my life.
I returned to the sailing camp the following year and reckoned that I knew how to sail; an assumption that was disproved four years later.
Now then, where was I? Oh yeah, in the garage.
To show what I’ve done around the gunwale I took some photographs and drew a diagram. I think that it’s important to make the gunwale as stiff as possible; with the original GRP deck in place it was virtually immovable because of the large horizontal area of the deck moulding bracing it. Now the stiffness will have to be provided by the wood laminations I have glued in place. So far there are four 10mm layers of soft wood around the gunwale, glued to the steel band on the outside of the hull, and to the GRP on the inside, with epoxy adhesive which has been just brilliant. There will be more wood, with a further 10mm thickness on the outside (possibly even hardwood - oak?) And a capping piece to run right along the top of the gunwale. Then I have to fix in a hefty member each side roughly amidships to support the rowing thwart and the rowlock sockets.
The next photo shows the hull starting to look a bit more like it with the wood in place around the gunwale - albeit with clamps.
There’s also a shot of the transom after I removed the old rudder mounting - a piece of hardwood which over the years had been eaten away by rot and what looked like worms.
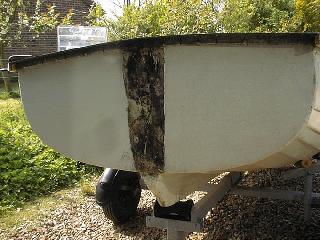
Here's some I took earlier - I've got to catch up a bit as this blog is almost a week behind the action.
This is the hull after removal of the deck. You can see that the mould must have been taken off an old dinghy. I've forgotten to mention that Lugg is ten feet long and four wide, with a pivoting centreplate and transom hung rudder.
And here's the deck moulding that I'm discarding. The more you see the boat without it the more you realise quite how ugly the deck was.
This shows the damage to Lugg's nose and the method of construction with the steel band around the top of the hull moulding.
And this shows how the steel band is fastened to the hull moulding with stainless screws and nuts. To avoid removing them and removing much of the rigidity from the hull moulding I epoxied strips of softwood 10 x 25 x 150mm between them on both the inside and the outside of the hull, to which I have subsequently glued a continuous strip of softwood 10 x 25 x 3,200mm. Diagram and picture to follow, but now the sun's shining and I've got to get on with it.
When I started to look at the boat I had bought I realised that although he was sound enough to be sailed as he was for the time being, he would need fairly major work in the near future. This became more obvious when I started to remove the nasty black rubber fendering around the gunwale. This was clearly an old boat (for GRP), and was constructed in an unusual fashion. Instead of the deck being bolted and glassed to a flange around the top of the hull as normally found in GRP boats, a piece of stainless steel angle had been bolted around the top of the hull to make a flange. My guess is that the hull moulding was originally designed to be finished with a wood gunwale and thwarts, but that it had been adapted to take a GRP deck with thwart and mast step moulded in. This would require less upkeep, always desirable in a hire boat. The horizontal part of the angle steel had been sawn through every eight inches so that the metal could be bent round the top of the hull moulding to form the flange - otherwise the metal simply would not bend. Here’s a sketch cross section of the hull/deck join:
Although this was odd construction it has meant that the hull has withstood the battering of the years pretty well. Although the hull moulding has been split and repaired a couple of times in the past (between waterline and gunwale, I’m glad to say) the hull has never lost shape due to any of these impacts, as the steel band is really strong. I have seen a dinghy similar to Lugg squashed between a forty foot hire cruiser and the wooden quay heading; the hull became about a foot narrower before the pressure was released, and although it more or less sprang back into shape, I would not have been happy if it had been my dinghy.
Anyway, Lugg was strong except in the deck. This had broken up around the rowlock sockets and been repaired several times, and as you can see from the photos the very front of the deck moulding simply wasn’t there any more. I decided to remove the deck, discard it, and replace it with a wooden one. This would look better - varnished wood instead of swimming-pool-blue GRP - and would enable me to alter the deck layout and attach fittings more easily. So I went for laminated wood gunwales and framing with a marine ply deck.
I went to our local specialist hardwood Timber Yard and nearly bought a plank of Mahogany 150 x 25mm x 4 metres long for the laminated parts; the bloke at the desk said it would cost me “about thirty quid” but when he came to measure it the price (with VAT) went up to fifty pounds. As one object of the exercise is to get afloat in a decent looking boat as cheaply as possible I decided to go with soft wood instead. From experience of my other wooden boats I knew that provided you choose the straightest and closest grained, most knot-free softwood and build and coat with modern epoxies durability is not a problem; and such woods can be stained to resemble mahogany or whatever. And they’re more environmentally friendly. So I spent seventeen pounds (and a lot of time selecting my pieces) on softwood and started to saw up 10mm wide strips for laminating.
Meanwhile the original deck was retained to provide measurements for positioning of rowlocks, mast step and seat.
With the acquisition of a dozen and a half clamps and the spending of another seventeen pounds on SP Systems 106 Epoxy, I was ready to begin.
And this is what I saw when I removed the fendering! Having been towed around behind 40 foot hire motor cruisers for the last three or four decades, Lugg has taken a bit of a pasting on the stemhead. There are about 16 different holes where the towing eye has been repeatedly ripped out of the GRP and replaced, new holes being drilled each time; these dinghies lead a very rough life. The very top of the stem is missing altogether. The repairs over the years were quick and dirty, since most of them will have been done between one hirer bringing the boat back at 10.00am on Saturday morning and a new hirer taking it out again at 4.00pm the same day. Doesn't make for craftmanship.
Taking off the black rubber fendering took about four hours - it was held in place by all 56 stainless steel nuts and bolts which held the deck on to the hull moulding. Every single bolt had been nipped off close to the rubber under the gunwhale, making it very difficult to remove the nut. You can see the detail in this photo.
This will, I hope, be an account of the rebuilding of a Norfolk Broads ex-hire fleet GRP lugsail dinghy.
I haven't owned a boat for four years and was beginning to get withdrawal symptoms, having had various dinghies and other sailing boats for the previous 24 years.
He needs quite a lot of work - the top of the stem has been bashed away to nothing over the years as a hire-cruiser tender, and there are cracks and scrapes at various places on the hull. The deck is knackered and will need some thought.
|